Supplier Management Introduction
Systems engineering (SE) is a key participant in managing suppliers. Clear and accurate requirements are necessary for successful supplier performance, as is the ability of those suppliers to direct their own suppliers.
Key suppliers will be involved in the full requirements process of analysis, allocation, and flow down. This will include requirements in the Procurement Specification, Statement of Work, Supplier Data Requirements List (SDRL), and any applicable specifications. The Systems Engineering Management Plan (SEMP) describes these SE processes, while the Supplier Management Plan (SMP) (NA-07-1379) describes how supplier management interacts with Boeing organizations (e.g., engineering [including systems engineering], program management, quality engineering) and with the suppliers. The SMP also defines the methods for maintaining records of supplier points of contact and their Boeing counterparts, and the means for maintaining communication between Boeing and suppliers. These means may include formal and informal correspondence, formal reviews and configuration audits, technical interchange meetings (TIMs), periodic telecommunications, and memoranda. However, all formal direction between OEM and the suppliers must flow through the supplier management organization. Risk management is also referenced in the SMP, particularly the extent to which suppliers are involved in the identification, analysis, and mitigation of risks applicable to their work and products. Quality, Materials, Processes and Standards (MP&S), and Supplier Management and Procurement (SM&P) representatives are included in the product teams to provide programmatic direction and to formally receive information from the supplier.
The SE team helps define the functional, performance, and interface requirements, and Specialty Engineering has the specific responsibility for defining selected sections of the Procurement Specifications and SOW tasks. SE is accountable for requirements allocation, product design integrity, and design to cost and affordability objectives. It is also the responsibility of the SE team to work with each product team to ensure that the prime contract requirements flow down in the Buy-to packages and are being met for each specific procurement activity. Systems and Specialty Engineering support the supplier selection process by defining evaluation criteria for their sections of the supplier proposals, helping score those criteria, and responding to supplier questions. They also perform technical evaluations of supplier documentation and products, participate in supplier milestone reviews, and evaluate supplier qualification and other reports.
Prior to issuing a contract to a software supplier, OEM Supplier Management will conduct a capability survey to establish that the supplier has a process capable of producing hardware
and/or software that meets the requisite requirements and that will also perform in-process compliance audits to ensure that the planned activities are occurring as required.
The product teams are responsible and accountable for implementing the management control strategy for the suppliers. Specific methods of control may vary by supplier, but the overall control plan focuses on five critical areas: technical performance, quality, cost, schedule, and risk/issue/opportunity management. All five affect the extent that a deficiency in one area may signal a potentially more serious problem in another. It may take several years to design and qualify supplier materials, and then to acquire them for production, aircraft installation, and provision of spares. As a result, SE participates in the assessment of Diminishing Manufacturing Sources and Material Shortages (DMSMS) and related obsolescence issues, to assure continued availability to the customer of the required functionality. SE is a key participant in the Production Readiness Review, when one is requested by the customer. SE also contributes to the evaluation of any changes to the supplier product that are deemed needed between the configurations that are initially qualified and those purchased for installation in production aircraft (Figs. 6.4.1 and 6.4.2).
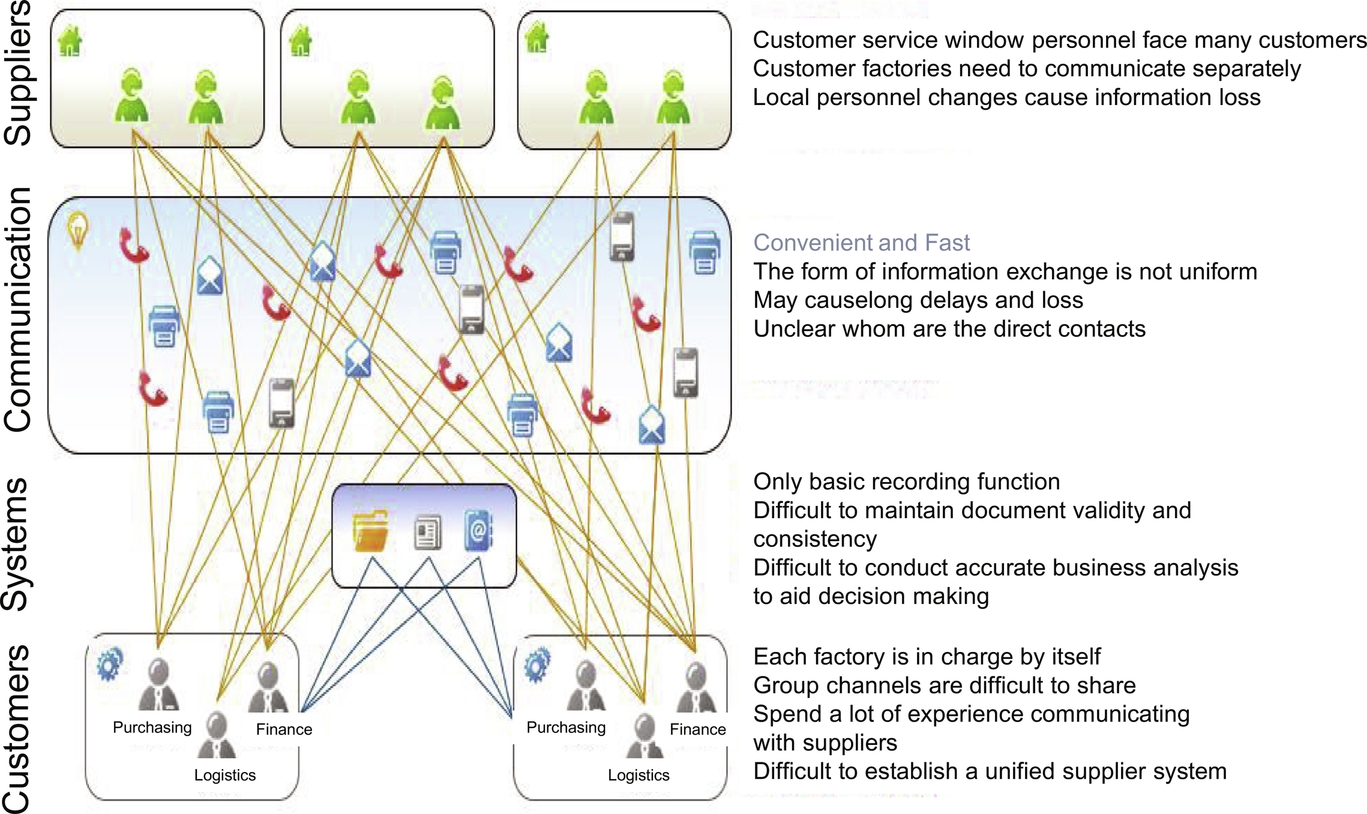
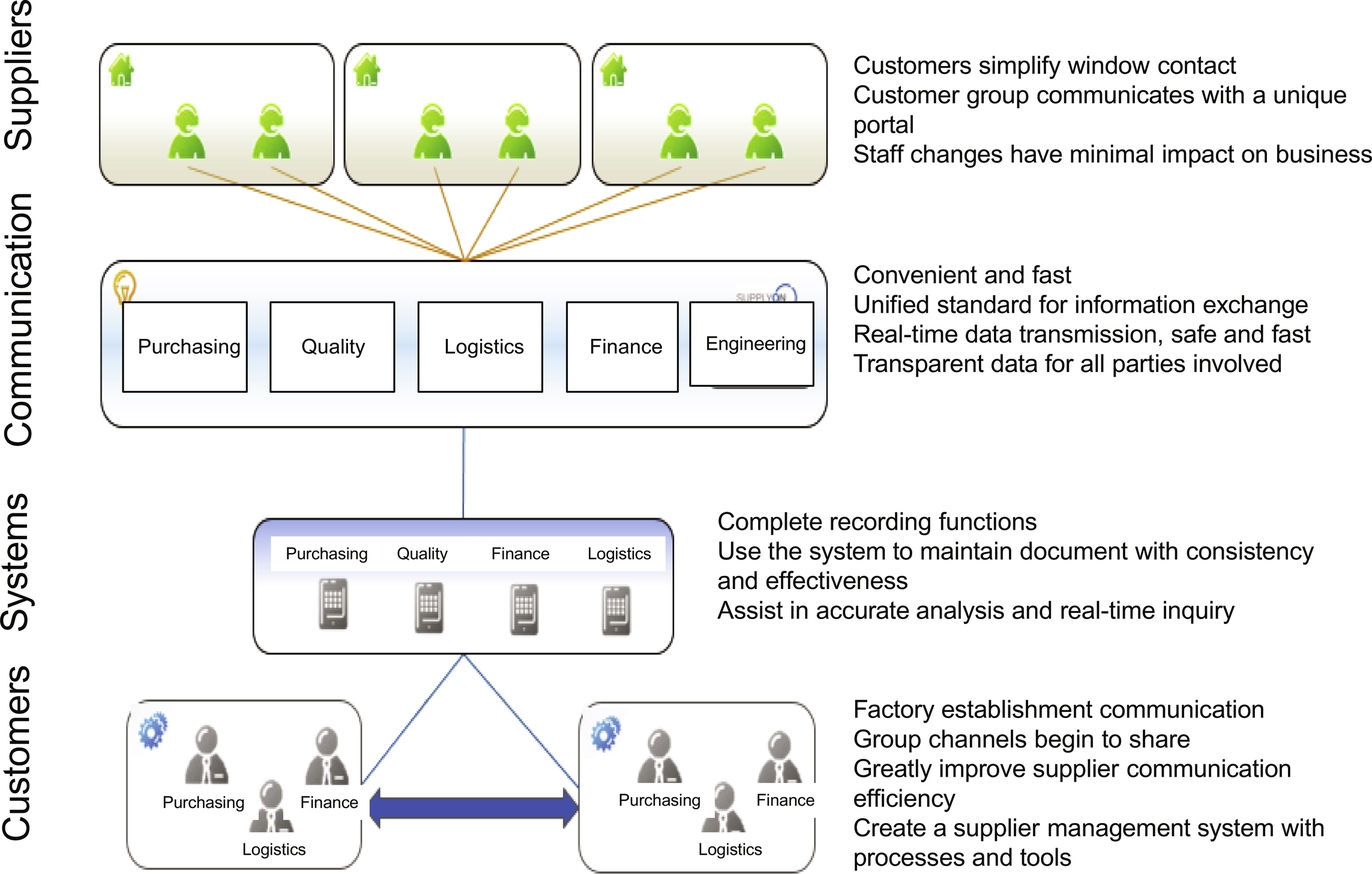
Supplier Performance Measurement Rating System
Boeing’s supplier1 ratings are based on a 12-month rolling average with three levels of visibility: site level (where the product is delivered), business-group level, and company level (a composite rating of the supplier). Suppliers are rated on three areas: delivery, general performance assessment (GPA), and quality.
Delivery refers to the percentage of pieces the supplier delivered on time to Boeing during a 12-month period. It measures performance against the scheduled due date of each purchase-order line item. Delivery also includes performance on consumption-based purchase orders, measured daily by the number of part numbers outside established inventory range (maximum and minimum) as related to total part number opportunities.
GPA provides a comprehensive assessment of a supplier’s business management performance on four distinct business models—Production (such as raw material and parts suppliers), Development (research, concept, and technology development suppliers), Support services (providers of spare parts, modifications, retrofits, training and product support), and Shared services (IT procurement, employee financial services and site-services suppliers). Boeing experts in supplier management, supplier quality, engineering, and finance evaluate and assess supplier performance in the areas of management, scheduling, technical issues, cost and quality. GPA evaluations consist of key performance indicators (KPI) unique to each category and business model evaluation. GPAs are conducted on key suppliers, which are identified based on who is in the top 50% of Boeing’s supply base dollars spent or on the business needs of specific program requirements.
Quality rating is determined by using one or more of the following methods based on the types of supplier products and services provided: traditional, value-based, and index-based. The traditional method is based on the percentage of pieces accepted (rejected quantity subtracted from the received quantity and divided by received quantity) from the supplier during a 12-month period. The value-based method considers the cost of product nonconformance subtracted from the price of products received during a 12-month period. This method is used for suppliers of complex parts, assemblies and kits, electronics, and major structures in which the traditional method does not make sense. The cost of nonconformance includes costs incurred from defect detection and resolution to corrective action. The index-based method relies on scorecard criteria of quality key performance indicators (KPIs) selected by Boeing and the supplier. This is used for service suppliers, system integrators, modification and maintenance programs, and programs that are in development or prototypes for which the traditional and value methods do not make sense. An example of a quality exception report is presented in Fig. 6.4.3.
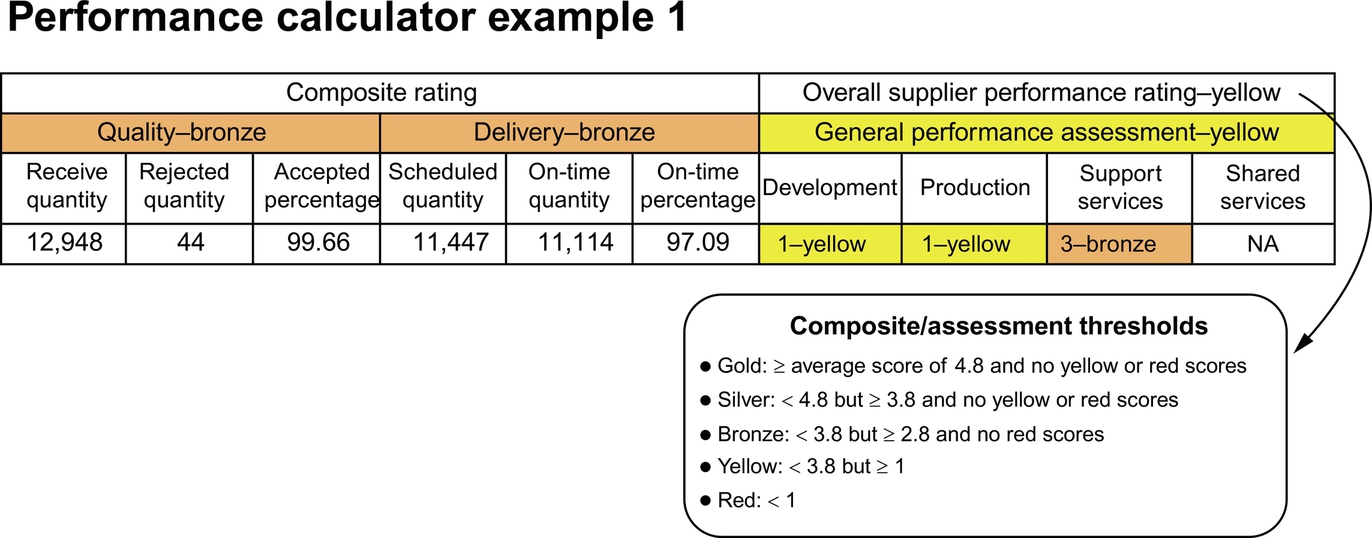
Suppliers are categorized into five color-coded threshold standards summarized in Table 6.4.1.
Table 6.4.1
Figs. 6.4.4 and 6.4.5 present two example scenarios with performance calculations.
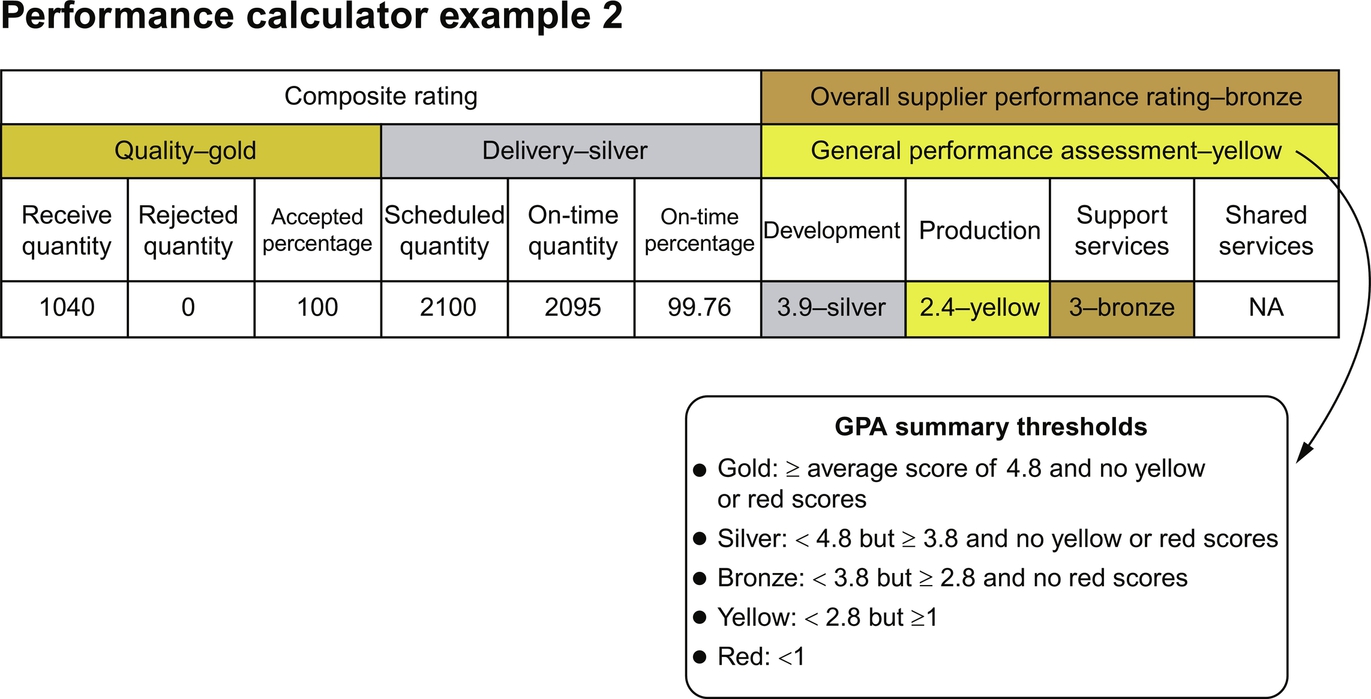
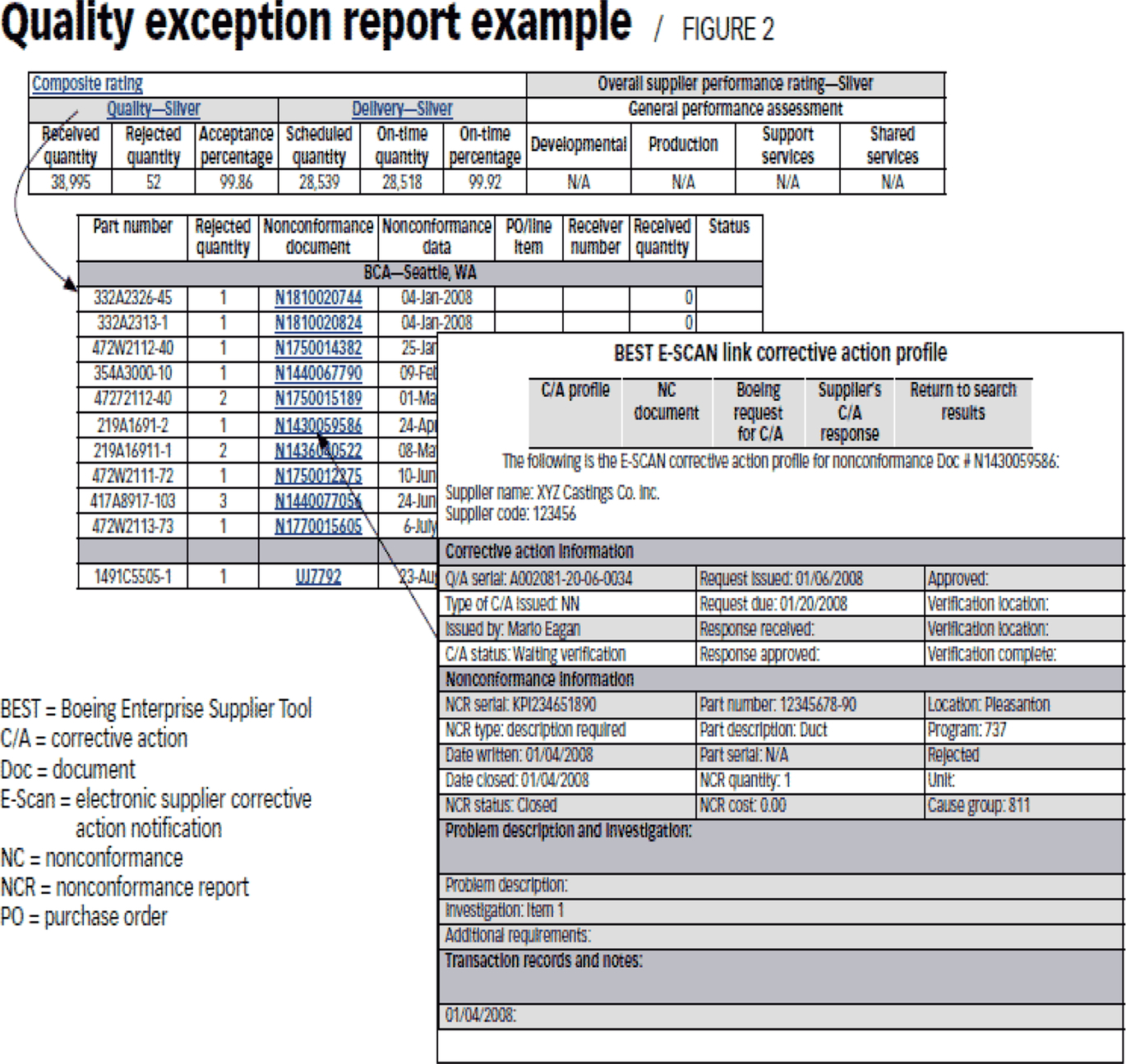
Summaries
Supplier Program Management (SPM) Responsibilities, Accountabilities, and Authorities (RAAs) are as follows:
- 1. Responsible for Supplier execution and product integrity;
- 2. Integrates and facilitates resolution of technical and business issues;
- 3. Establishes and evaluates performance measures, metrics, and leading indicators;
- 4. Accountable for Supplier Improvement Plan and actions.
Collaborates with Supplier to understand their capabilities related to program requirements and future growth.
Leave a Reply