The Work Breakdown Structure (WBS) is the basis for project planning and control; a project manager must have a WBS in order to plan and measure progress. So that the specified tasks can be performed, the WBS is at its core a hierarchical breakdown of the work that needs to be performed by the project team (see Fig. 4.3.1). The WBS is used for estimating time schedule, cost, and resources required for a project.
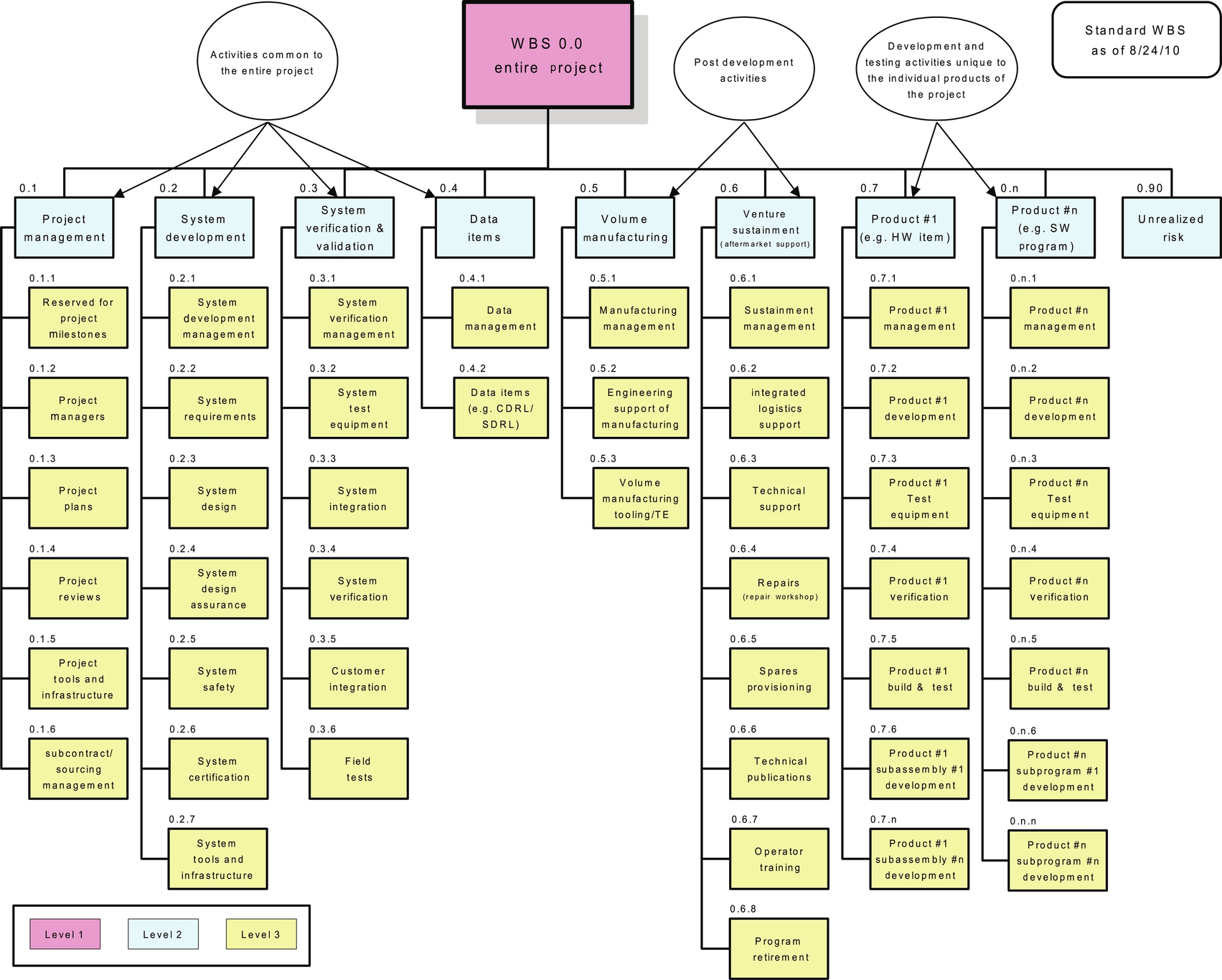
The Organizational Breakdown Structure (OBS), in large organizations, helps the project manager understand how the organization is structured and operates and it relates the work tasks to meet the schedule that is promised to the customers.
The Product Breakdown Structure (PBS) is a hierarchical structure in which the main output of the project is placed at the top level. The next level down shows the components that make up the higher level. This process continues to the level of individual products. Each product will have defined acceptance criteria and quality control methods.
Fig. 4.3.2 shows how to establish a project budget baseline.
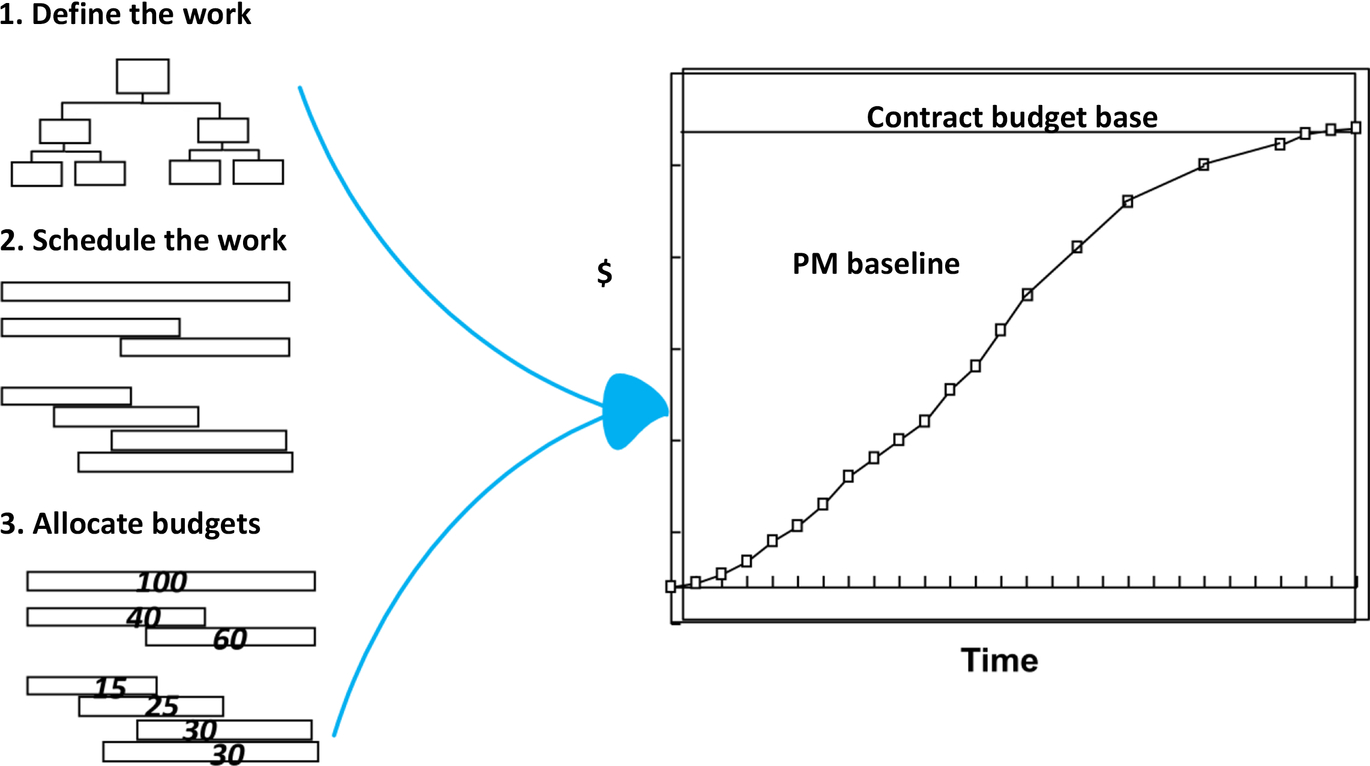
Fig. 4.3.3 depicts the use of WBS and OBS to complete planning and execution. The Responsibility Assignment Matrix (RAM) is created by the WBS and OBS.
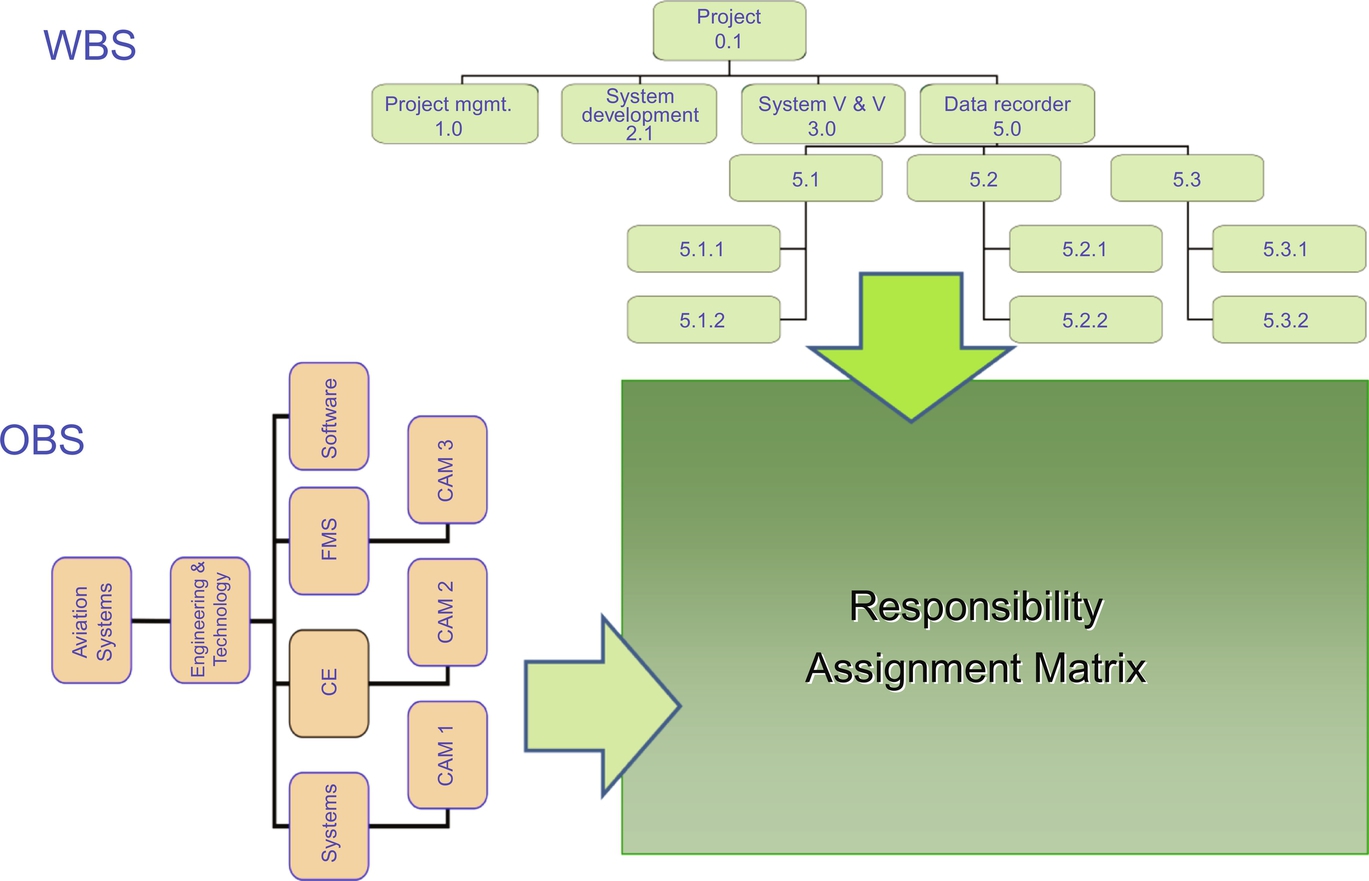
There are two ways to allocate budgets to the lowest level. One method is top-down (see Fig. 4.3.4) and the other is bottom-up (see Fig. 4.3.5). The budget allocation starts, in general, with the bottom-up method and finishes with the top-down method. The total budgets submitted from each division are usually larger than the allocable budget to the program. This is because the Program Budget Control Office holds a certain percentage of the total budgets as a planned profit for the company and as an MR budget, the amount of the budget withheld for management control purposes. The Program Budget Control Office reviews the division budgets against the allocable budgets and forwards the adjusted budgets to each division. The division business management provides a budget information guideline and the adjusted budgets to each department or group. The Cost Account Manager (CAM) then reallocates the adjusted budget to the cost account.

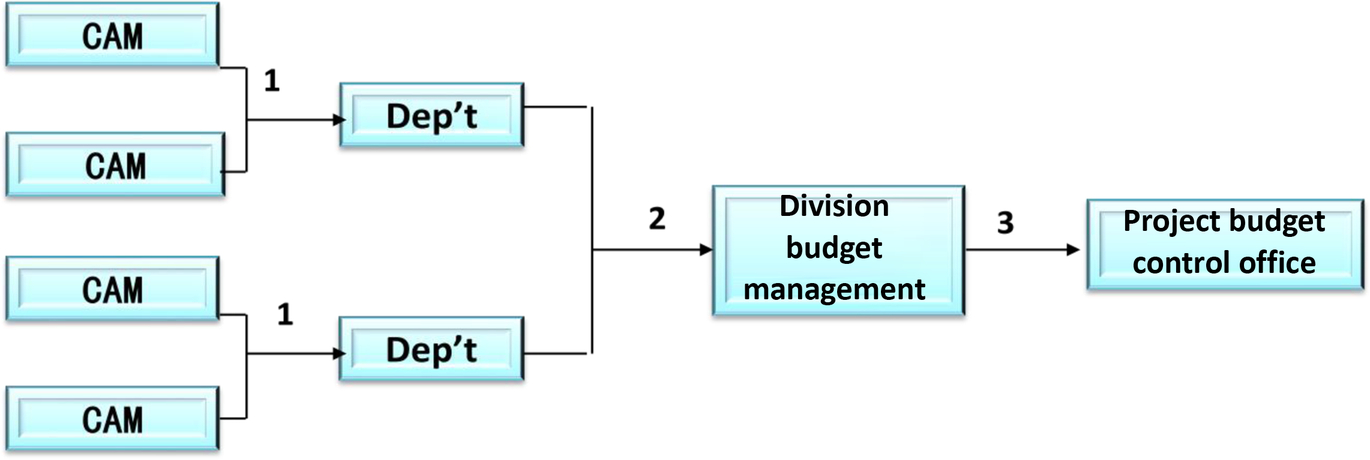
The top-down method is described in Fig. 4.3.4.
- 1. Cost Account Managers (CAMs) prepare Budget Packages (Statement of Work, Time-phased budgets, Schedule, etc.).
- 2. The Division Budget Management reviews the packages and sums up the budget at the Department level.
- 3. The Department budgets are totaled to the Division budgets.
- 4. The Project Budget Control Office reviews the Division budgets and approves them.
The bottom-up method is described in Fig. 4.3.5.
- 1. Cost Account Managers (CAMs) prepare Budget Packages (Statement of Work, Time-phased budgets, Schedule, etc.).
- 2. The Division Budget Management reviews the packages and sums up the budget at the Department level. The Department budgets are totaled to the Division budgets.
- 3. The Project Budget Control Office reviews the Division budgets and approves them.
These EVMS formulas (Fig. 4.3.6 and Table 4.3.1) are not “tricks.” They are additional tools that allow us to:
- 1. Recognize the conditions of the environment
- 2. Change the receptor (receiver or the people will be using EVMS)
- 3. Modify our own reaction and outcomes by taking advantage of the EVMS tool benefits, including more efficiency and better program tracking
- 4. Plan and execute programs successfully and become leaders!
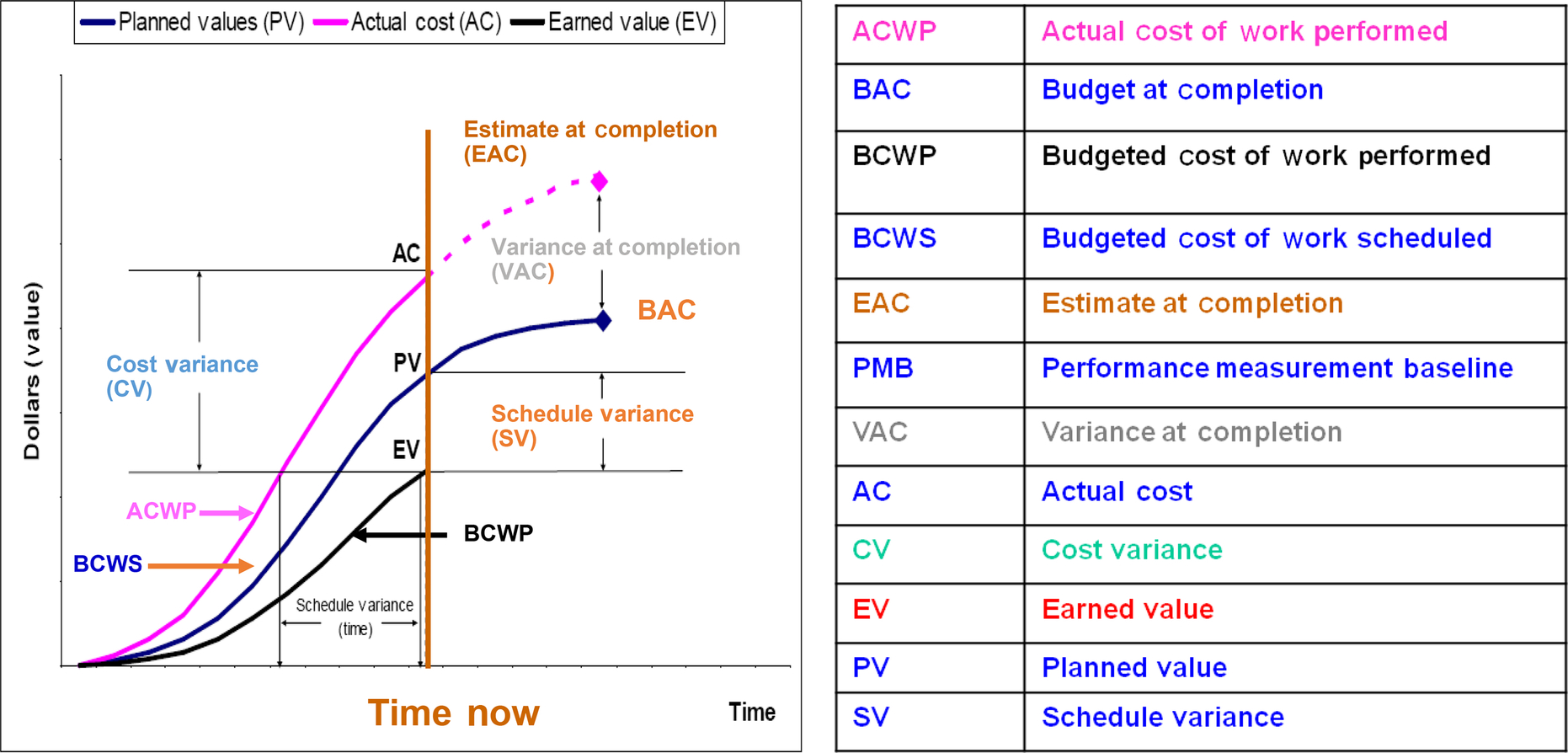
Table 4.3.1
![]() |
Leave a Reply