The main constituents in the manufacture of cement, as discussed earlier, are lime, silica, alumina and iron oxide (Table 6.1).
These oxides interact with one another in the kiln at a high temperature, and more complex compounds are formed. The relative proportions of these oxides are fully responsible for the various properties of cement, rate of cooling and fineness of grinding.
Out of the complex compounds formed in the kiln at the high temperature, four compounds, viz., tricalcium silicate, dicalcium silicate, tricalcium aluminate and tetracalcium aluminoferrite. The chemical formula and abbreviated formula are presented in Table 6.2.
Table 6.2 Major complex compounds
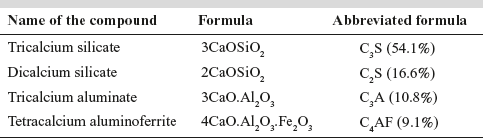
As the four compounds mentioned above were first identified by Mr R. H. Bogue, they are called Bogue’s compounds.
The abbreviated notations stand for
C for CaO
S for SiO2
A for Al2O3
F for Fe2O3
Of the four compounds tricalcium silicate and dicalcium silicate are the compounds which contribute towards strength. Both the compounds put together constitute about 70–80% of cement. In modern cement, the average C3S content is 45% and that of C2S is about 25%.
Apart from the four major compounds some minor compounds also form in the kiln, viz., K2O and Na2O.
The percentage of the four major compounds present, in general, in cement based on Bogue’s concept is shown in brackets in Table 6.2.
When water is added to cement, these four compounds react in the decreasing order as C3A, C4AF, C3S and C2S.
During the initial period of hardening the strength gain of C2S is small and is about 15% as that of C3S. After 28 days, the hydration of C3S comes practically to an end. The hydration of C2S begins only after the full hydration of C3S. The hardening of concrete is greatly speeded up by C3A.
Leave a Reply