In continuous kilns, the process of burning is continuous. There are three types of continuous kilns, viz.,
- Bull’s Trench Kiln
- Tunnel Kiln
- Hoffman’s Kiln
(i) Bull’s Trench Kiln
This type of kiln is usually oval in plan and is constructed in a trench excavated in the ground. It may be fully underground or partly projecting above ground. The depth of trench is about 2 metres. The outer and inner walls are constructed of bricks, and the flue holes are provided in the outer walls (Fig. 3.6). Dampers are provided to conveniently divide the kiln into sections.
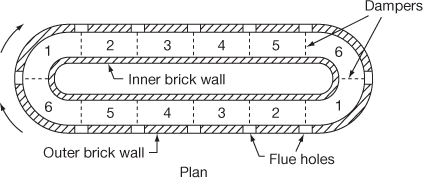
1. Loading 2. Empty 3. Unloading 4. Cooling 5. Burning 6. Heating
Figure 3.6 Bull’s trench kiln
Bricks are arranged in sections in such a way that flues are formed. Fuel is placed in the flues, and the top surface is covered with earth and ashes to prevent the escape of heat. The fuel is burnt through the flue holes. Additional flue holes are provided at the top to insert fuel when burning is in progress. Two movable chimneys are used to form a draught. These chimneys are placed before the section is fired. This arrangement makes the hot gases leaving the chimney warm up the bricks in the next section. When the burning is over in a section the flue holes are closed and the bricks are cool down gradually. The fire is advanced to the next section and the chimneys are moved forward.
As loading, burning, cooling and unloading are carried out simultaneously, a continuous supply of bricks is available. This is the mostly used kiln in India.
(ii) Tunnel Kiln
This kiln is in the form of a tunnel which may be of any shape in plan, viz., straight, circular or oval. The zone of fire is at one place. The moulded bricks are loaded on a trolleys, which are moved from one end of the tunnel to the other end. During this process when they approach the zone of fire that are completely dried and pre-heated.
These bricks are burnt in the zone of fire and are then moved for cooling. After adequate cooling, the bricks are unloaded. As the temperature can be controlled, better quality bricks are produced. The bricks from this kiln are said to be economical.
(iii) Hoffman’s Kiln
This is constructed over the ground to produce a continuous supply of bricks on a large scale.
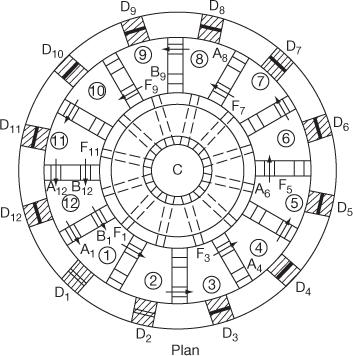
D1 to D12 – Main doors; D1 and D2 – Opened doors, D3 to D12 – Closed doors
1 to 12 – Chambers; C – Chimney, F1 to F12 – Radial flues
A1 to A12 and B1 to B12 – Communicating doors
Figure 3.7 Hoffman’s continuous kiln
This is circular in plan and is provided with a chimney at the centre. Around the chimney are 12 chambers that are in an annular shape. Each chamber comprises of the following parts (Fig. 3.7):
- A main door for the loading and unloading of bricks (e.g. D1).
- Communicating doors for the flow of flue gases between the chambers (e.g. A1 and B1).
- A radical flue from each chamber to the chimney (e.g. F1).
- Fuel holes for providing fuel, and powdered coal is used as fuel.Functions that occur in the chambers are listed below:Chamber 1 – LoadingChambers 9–12 – Drying and pre-heatingChambers 7 and 8 – BurningChambers 3– 6 – CoolingChamber 2 – Unloading
The working of a kiln is as follows:
- Cool air enters through Chambers 1 and 2 as they are open doors.
- It crosses the cooling Chambers 3–6 and enters the burning Sections 7 and 8 in a heated condition.
- It moves to Chambers 9–12 to dry and pre-heat the raw bricks.
- It escapes into the atmosphere through the damper of Chamber 12 and the chimney.
The flow of air and fuel gas are shown by arrows in each chamber. Although the initial cost is more, Hoffman’s Kiln claims several advantages:
- High-quality bricks with uniform burning are obtained with regulation of heat.
- Supply of bricks are continuous in all seasons because the top of the kiln is closed, and the working is not stopped.
- Considerable saving in fuel due to pre-heating of raw bricks by fire gases.
- No air pollution in the locality, as the exhaust gases do not contain black smoke or dust particles.
Leave a Reply