Two types of hand moulding, viz., ground moulding and table moulding, are adopted in India. In hand moulding, bricks are moulded manually. This is preferred in areas where the manpower is cheap and available readily and where only a small quantity of bricks is needed.
(i) Ground Moulding
The process of moulding bricks on the ground by manual labour is called ground moulding. At first a level ground is prepared, and a thin layer of fine sand is spread over the ground.
The mould is wetted and placed on the ground firmly. The tempered brick earth is dashed into the mould. The earth is pressed in the mould such that the earth fills all the corners of the mould without leaving any air gap within the brick. The excess earth is removed using a wooden or metal strike dipped in water.
The mould is then lifted, and the raw brick is left on the ground. The mould is cleaned, dipped in water and placed near the previous brick; the process is repeated till the ground is completely covered with the prepared raw bricks. On an average, a moulder can mould about 750 bricks per day. When the bricks have sufficiently dried they are taken to the drying shed and placed in an ordered manner.
Brick prepared by dipping moulds in water every time called slop-moulded brick, and if sand is sprinkled on the sides of the mould, the brick is called a sand-moulded brick.
(ii) Table Moulding
Table moulding is done on a table of size 2 m × 1 m × 0.7 m instead of on the ground. The process of moulding is almost similar to ground moulding except for a few changes.
Invariably, table-moulded bricks are provided with a frog. A frog is a mark of depth of about 10 to 20 mm provided in a mould. This serves two purposes, viz., it provides a key for the mortar when the next brick is placed with its flat surface over this and to place the trademark of the manufacturer.
A stock board of the same site as the inside dimensions of the mould with a projection for the frog with the trademark of the manufacturer is kept on the moulding table, and the moulder stands behind the table.
The mould is placed to fit the stock board and the tampered earth is dashed against the mould, carefully filled, and excess earth is removed. Then a thin board called the pallet board is placed on the mould; the mould and pallet board are lifted together followed by lifting the mould leaving the brick on the pallet board. Another pallet board is kept on the brick and carried to the drying yard where it is placed on its edge and the pallet boards are removed. This procedure is repeated. Figure 3.3 shows a moulded brick lying over the pallet board.
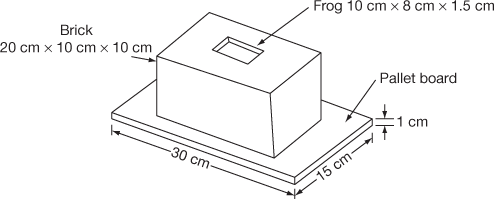
Figure 3.3 Moulded brick lying over the pallet board
Leave a Reply