When a discharge takes place between two points of the anode and the cathode, the intense heat generated near the zone melts and evaporates the materials. For improving the effectiveness, the workpiece and tool are submerged in a dielectric fluid as shown in Figure 23.9. It has been observed that both the electrodes are made of the same materials; the electrode connected to the positive terminal generally erodes at a faster rate due to the following reasons:
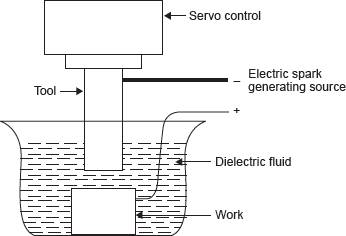
Figure 23.9 A Conceptual Diagram for EDM
- The momentum with which the stream of electrons strikes the anode is much more than that due to stream of the positive ions impinges on the cathode though the mass of an individual electron is less than that of the positive ions.
- The pyrolysis of the electric fluid creates a thin film of carbon on the cathode.
- A compressive force is developed on the cathode surface.
For these reasons, the workpiece is normally made the anode. A suitable gap, known as the spark gap, is maintained between the tool and the workpiece surface. The sparks are made to discharge at a high frequency with a suitable source. Since the spark occurs at the spot where the tool and the workpiece surfaces are the closest and the spot changes after each spark (because of material removal after each spark). The sparks travel all over the surface, and finally the workface conforms to the tool surface. Thus, the tool produces the required impression in the workpiece.
For maintaining the predetermined spark gap, a servo control unit is generally used. The gap is sensed through the average voltage across it and this voltage is compared with a preset value. The difference is used to control servomotor. The range of spark frequency is 200–500,000 Hz, the spark gap is 0.025–0.05 mm, and the peak voltage is 30–250 V. The maximum metal removal rate can be 300 mm3/min.
Inaccuracy in EDM
- Taper of the hole or pocket machined: A taper results because the upper portion of the hole wall is subjected to a more number of sparks than the bottom portion. It can be controlled by an appropriate alteration of the electrical parameters.
- Overcut due to the sparks at the side faces of the electrode: An overcut is that dimension by which the hole in the workpiece exceeds the electrode size. The magnitude of overcut depends on the spark length and, to some extent, on the crater dimensions.
- Errors due to gradual change in the electrode (tool) shape and size.
Selection of Electrode Materials
The selection of electrode material depends on the following factor:
- Material removal rate.
- Wear ratio.
- Ease of shaping the electrode.
- Cost.
Dielectric Fluids
The basic requirements of an ideal dielectric fluid are given below:
- Low viscosity.
- Absence of toxic vapours.
- Chemical neutrality.
- Absence of inflaming tendency.
- Low cost.
Advantages
- There is no work distortion.
- All electrical conductors irrespective to its hardness can be easily machined.
- It gives high accuracy.
- Fine hole can be easily drilled.
Applications
This process is very useful in tool manufacturing due to ease with which hard metals and alloys can be machined. Other application includes resharpening of cutting tools and broaches, trepanning.
Leave a Reply