Laser (Light Amplification by Stimulated Emission of Radiation) is a highly coherent (in space and time) beam of electromagnetic radiation with wavelength varying from 0.1 to 70 mm. However, the power requirement for a machining operation restricts the effectively usable wavelength ranges to 0.4–0.6 mm. Because of the fact that the rays of a laser beam are perfectly parallel and monochromatic, it can be focused to a very small diameter and can produce a power density as high as 107 W/mm2, for developing a high power; normally a pulsed ruby laser is used. The continuous laser CO2–N2 has also been successfully used in machining operations.
A coiled xenon flash tube is passed around the ruby rod and the internal surface of the container walls is made highly reflecting so that maximum light falls on ruby rod for the pumping operation as shown in Figure 23.8. The capacitor is charged and very high voltage is applied to the triggering electrode for initiation of flash. The emitted laser beam is focused by a lens system and the focused beam meets the work surface, removing a small portion of material by vaporization and ablation. A small fraction of metal is vaporized so quickly that a substantial mechanical impulse is generated throwing out a large portion of liquid metal. Since the energy released by the flash tube is much higher than the energy emitted by the laser head in the form of a laser beam, the surface must be properly cooled.
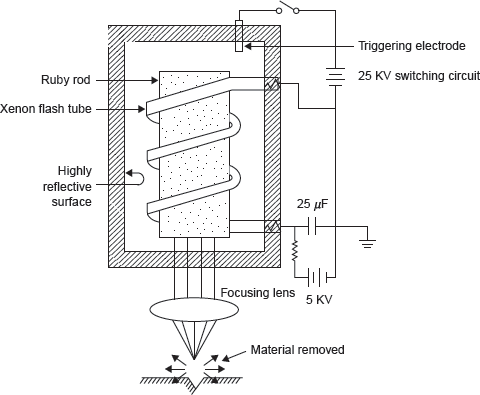
Figure 23.8 A Circuit for LBM
The efficiency of the LBM process is very low (about 0.3–0.5%). The typical output energy of a laser is 20 J with pulse duration of 1 ms. The peak power reaches a value 20,000 W. The divergence of the beam is around 2 × 10–3 rad, and using a lens with a focal length of 25 mm, the spot diameter becomes about 50 μm. Like the electron beam it is also used for drilling a micro hole up to 250 μm with accuracy of ± 0.025 mm when the workpiece thickness is more than 0.25 mm, a taper of 0.01 mm per mm is observed.
Advantages
- No tool wear occurs.
- Irrespective of material properties, all metal and non-metal can be machined.
- There is no deflection of the laser beam even for larger distance.
- There is negligible distortion of the material. Magnetic material can be cut or welded without losing the magnetic properties.
- Micro sized drilling, which is difficult to machine on refractory material, can be done easily.
- Beam size and the exposed area can be controlled easily.
Limitations
- High initial cost is required.
- Short life of flash lamp; safety procedures are to be followed strictly.
- It has low efficiency and low material removal rate.
- It is unable to drill deep hole.
- Drilled hole is always tapered in LBM.
- There is no possibility of machining plastic-like material due to burning of the material.
Applications
- It can be applied for micro drilling and engraving on the hard and difficult material.
- It can be applied for mass micro machining production.
- It can be applied for selective heat-treating of material.
- It can be applied in spectroscope, metallographic sciences, medical science, and photography.
Leave a Reply