Electron beam machining is also a thermal process of material removal. Here, a stream of high-speed electrons impinges on the work surface whereby the kinetic energy, transferred to the work material, produces intense heating. Depending on the intensity of the heat thus generated, the material can melt or vaporize. Very high velocity of electron beam can be obtained by using enough voltage and it can be focused on a point of diameters of 10–200 μm. The power density on such a small area is very high and it may go up to 6,500 billion W/mm2. Such a high power density can evaporate the material immediately.
In EBM, the electrons are emitted from the cathode (a hot tungsten filament), the beam is shaped by the grid cup, and the electrons are accelerated due to large potential difference between the cathode and the anode as shown in Figure 23.7. The beam is focused with the help of electromagnetic lenses. The deflecting coils are used to control the beam movement in any required manner. In case of drilling holes, the hole diameters depend on the beam diameter and energy density. When the diameter hole required is larger than the beam diameter, the beam is deflected in a circular path with proper radius. A small crater on the beam incident side of the work characterizes most holes drilled by EBM. The drilled holes also posses a little taper (2°–4°) when the sheet thickness is more than 0.1 mm.
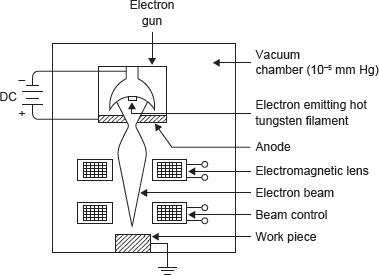
Figure 23.7 A Circuit for EBM
Advantages
- No burr is produced.
- There is no heat affected area.
- No machining stresse is set up.
- This is one of the fastest methods of metal removal on tough alloys.
- It is especially useful in cutting slots, deep holes of small diameter, etc., in hardened steel or difficult to cut alloys of complex shapes.
- It has excellent repeatability.
- Very close tolerances (0.02 mm) can be obtained.
- Finish obtainable is of the order of 0.1–4 mm. (for better finish high feed rates and high amperages are required; finish also depends upon material to be machined, e.g., aluminium always has matte finish and cobalt gets a polished surface on machining by ECM).
Disadvantages
- Initial cost of machine set up and tooling is high.
- It requires complex electrodes and flushing arrangement.
- It requires high power consumption.
- Machining requires vacuum of 10-5 mmHg.
Applications
- This is a very effective method for machining of materials of low heat conductivity and high melting point.
- It is used for micro machining operations on workpieces of thin section.
- It is used for micro drilling operations (up to 0.002 mm) for thin orifices dies for wire drawing, parts of electron microscopes, fibre spinner, injector nozzles for diesel engines, etc.
Leave a Reply