In the welding technique, a stream of high-speed electrons strikes on work surface where the kinetic energy of electrons transferred to the work material produces intense heat. The metal can melt or vaporize depending on the intensity of heat generated. The same process is also used for machining purposes.
The electron beam is produced in a high vacuum environment by an electron gun, usually consisting of a tungsten or tantalum cathode, a grid or forming electrode and anode as shown in Figure 20.48. A stream of electrons coming out from cathode are accelerated to high velocity and shaped into a beam by the potential difference between cathode and anode. The beam is collimated and focused by passing through the field of an electromagnetic lens. The focused area is 0.25–1 mm diameter and power density of 10 kW/mm and voltage 20–200 kV. This is sufficient to melt and vaporize any metal. The entire operation is carried out in a vacuum to prevent tungsten filament from oxidation, to prevent the scattering of electrons from air molecules, and to prevent the weld from atmospheric contaminations.
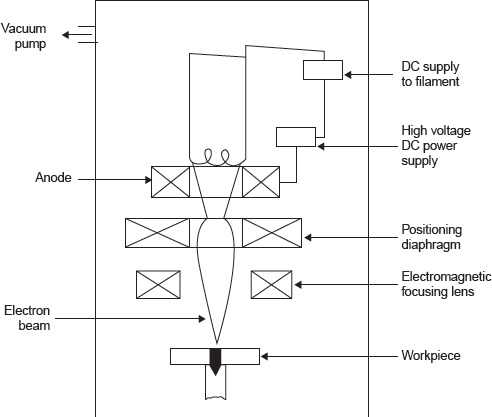
Figure 20.48 Electron Beam Welding
Advantages
- Depth-to-width ratio is very high (up to 25:1). This is possible because the process confines the heat to a narrow area.
- No shielding gas, flux, or filler material is required.
- Higher welding speed is possible.
- Dissimilar metals can be joined effectively as similar metals.
- Distortion and shrinkage in the weld area is minimal.
- Heat-sensitive materials can be welded without damage to the base metal.
Disadvantages
- The equipment is costly.
- Wide gap cannot be filled economically by this process.
- Vacuum is essential for the entire process.
- Joint preparation is essential because of the deep and narrow weld profile.
Leave a Reply