A highly ionized gas is known as plasma. In a plasma arc welding, arc is created between a non-consumable tungsten electrode and workpiece. A water-cooled copper nozzle surrounds tungsten electrode, which is used as cathode as shown in Figure 20.41. A gas (inert gas) like argon is supplied surrounding the tungsten electrode. The gas is forced through the orifice, where it is heated to high temperature through resistance heating and forms plasma. Plasma is ionized hot gas. It conducts electricity. The temperature of plasma gas may be as high as 33,000°C, which is sufficient to melt any workpiece. The copper nozzle is water cooled. A supplementary shielding gas may be used if required. The heat is transferred through the plasma to workpiece.
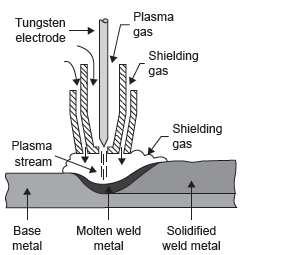
Figure 20.41 Plasma Arc Welding
There are two methods of plasma arc welding—transferred type and non-transferred type. In transferred type, tungsten electrode acts as cathode and workpiece as anode. The arc is transferred from cathode to anode. In non-transferred type, tungsten electrode acts as cathode but copper nozzle acts as anode and arc is not transferred to workpiece. The heat is carried to the workpiece by plasma gas. This method creates high noise during welding (100 dB). But it is a fast method and suitable for a number of metals.
Advantages
- High heat concentration results in high welding speed.
- It has improved arc stability.
- It minimizes thermal distortion.
- It has lower width-to-depth ratio of the weld.
- The focused heat of plasma results in narrower weld, less heat effected zone, and deeper penetration.
Limitations
- The equipment is very expensive, approximately five times more than TIG equipment.
- Long arc length results in excessive production of ultraviolet and infrared radiations which can harm the skin.
- Gas consumption is high.
- Noise level is very high approximately 100 dB which is more than the permissible limit of 80 dB.
- Nozzle needs frequent replacement.
Leave a Reply