This welding process is very similar to MIG welding except that a blanket of granular, fusible flux shields the metal arc during the welding operation instead of inert gas. A bare electrode is fed through the welding head into the flux as shown in Figure 20.38. The arc is started either by striking the electrode on the work beneath the flux or initially by placing some conductive medium like steel wool beneath the electrode. The intense heat melts the flux and produces a pool of molten metal in the joint. The slag floats on the top of molten metal, forming a blanket, which eliminates spatter loss and protects the welded joint from atmospheric contamination or oxidation. This process uses AC or DC, high current 300–4,000 A. It is not suitable for the plate of thickness less than 8 mm and for vertical or overhead welding. The metals which can be welded by this process are carbon steel, alloy steel, stainless steel, nickel, copper, etc. It is not suitable for aluminium and magnesium alloys.
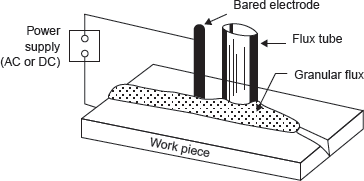
Figure 20.38 Submerged Arc Welding
Advantages
- Since the arc is completely hidden under a blanket of flux, there is no flash, spatter, or smoke.
- Very high current can be used. In conventional welding, where the arc is exposed, current above 300 A must be used with care due to high intensity of infrared and ultraviolet light rays. No such problems arise in this process due to arc covered with flux.
- It gives high deposition rate and deep penetration due to high current used in the process.
- High welding speed is possible.
- The quality of the weld is very good because of high cleanliness of the process.
Limitations
- It is largely limited to flat position welding.
- This process is not suitable for high-carbon steels, tool steels, aluminium, magnesium, titanium lead, or zinc because of numerous factors including unavailability of suitable fluxes, reactivity at high temperature, and low sublimation temperature.
- It is normally not suitable for welding of the metal plate of thickness less than 8 mm because of chance of burning.
- Possible contamination of the flux by moisture can lead to porosity in the weld.
- Other limitations include extensive flux handling and removal of large volume of slag.
- There is large heat affected zone.
Leave a Reply