In MIG welding, a high current density is supplied to the electrode and workpiece. Carbon dioxide gas or any inert gas like helium or argon is supplied to protect the weld pool. The electrode used is consumable and is in the form of wire. Automated feed of the wire is used as shown in Figure 20.36. The welding current is used in the range of 100–300 A. In this welding process, metal transfer rate is very high. Therefore, it is generally used for welding of thick plate. The metals welded by MIG welding are alloy steel, stainless steel, copper, brass, aluminium, magnesium, nickel, lead, silver, tungsten, etc. The current used is direct current and voltage is constant-arc voltage (CAV). Electrode is used as positive pole and work as negative pole.
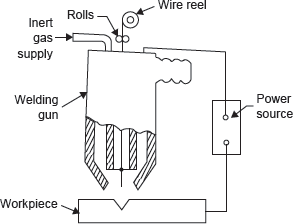
Figure 20.36 Metal Inert Gas Arc Welding
Advantages
- The rate of weld deposition is very high.
- Quality of the weld is good due to transfer of molten metal under protection of inert gases.
- No frequent change of electrode is required.
- No flux is required; therefore, no slug forms over the weld. This makes the process cleaner.
- It is versatile process and can be used on both light and heavy gauge structural plates.
Limitations
- The cost of equipment and consumable wire is much higher as compared to shielded arc welding.
Leave a Reply