Sand is the most suitable material for expandable mould. It has sufficient properties of moulding materials such as refractoriness, permeability, flowability, adhesiveness, cohesiveness, etc. Sand casting is the most versatile and common form of casting. In this method, a mould of sand with binding materials and water is prepared in which molten metal is poured and allowed to solidify. The entire casting process can be represented as a chain as shown in Figure 20.3.
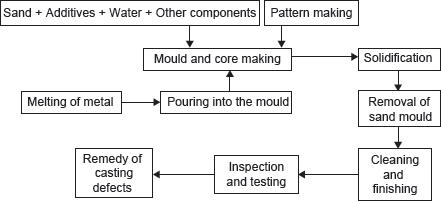
Figure 20.3 Steps in Sand Casting
A green sand mould is prepared with the help of pattern. The green sand is mixture of green sand, binders, and water. The pattern is made of wood plastics, metal, wax, etc. The selection of pattern materials is based on the type of casting process.
After pattern/mould making, metal is melted in the cupola or in other suitable furnace. The molten metal is poured into the mould cavity. The solidification process allows the product to gain the desired properties and strength. The shrinkage in casting is controlled by the riser and proper design of the mould. After solidification, casting is removed from the mould and sent to cleaning, finishing, and inspection. Finally, the casting defects are rectified.
Leave a Reply