This device is used to transmit the power from one shaft to another. The driver shaft carries a pump with radial vanes and the driven shaft carries runners (Figure 9.30). Both of these are enclosed in a casing filled with oil of required viscosity. The pump accelerates the oil by imparting energy to it. The oil is directed to hit the runners of driven shaft where the energy is absorbed and the oil is decelerated. The decelerated oil now enters the pump and the cycle is repeated continuously. The oil transfers the energy from the driver shaft to the driven shaft. As there is no mechanical (rigid) connection between the shafts, stock loads or vibration will not be passed on from one to the other. The runners will start rotating only after a certain level of energy picked up by the oil from the pump.
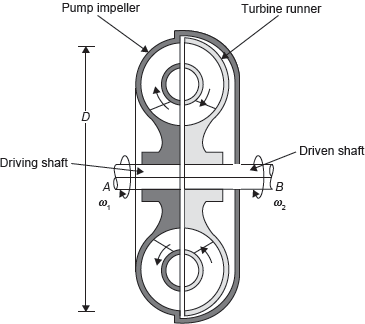
Figure 9.30 Hydraulic Coupling
Thus, the prime mover can pick up speed with lower starting torque before the power is transmitted. The vanes and runners cannot rotate at the same speeds. In case these do run at the same speed, there can be no circulation of oil between them as the centrifugal heads of the pump and turbine are equal, and no energy will be transferred from one to the other. The ratio of difference in speeds to the driver speed is known as slips, S.

where ωp is the driver shaft’s speed and ωT is the driven shaft’s speed.
Leave a Reply